Stress and Strain Definition
Stress in physics is the internal resistance within a material when subjected to an external force, quantified as force per unit area. It measures the material’s ability to withstand deformation. Strain is the resulting deformation, expressed as a fractional change in size or shape, and is a measure of the material’s response to stress. The knowledge of strain and stress in Physics enables students to identify strengths, deformations, and other important parameters affecting objects.
Explanation
In physics, stress and strain are fundamental concepts used to describe the behaviour of materials under the influence of external forces. Stress is a measure of the internal resistance a material offers when subjected to an external force. It is quantified as the force applied per unit area and can be viewed as a material’s ability to withstand deformation. Stress can manifest in various forms, such as tensile stress, which stretches a material, or compressive stress, which compresses it.
Strain, on the other hand, is the resultant deformation that occurs in response to stress. It is expressed as the fractional change in size or shape relative to the material’s original dimensions. Additionally, strain provides insight into how much a material distorts under the influence of stress and can be categorized as either tensile strain (elongation) or compressive strain (contraction).
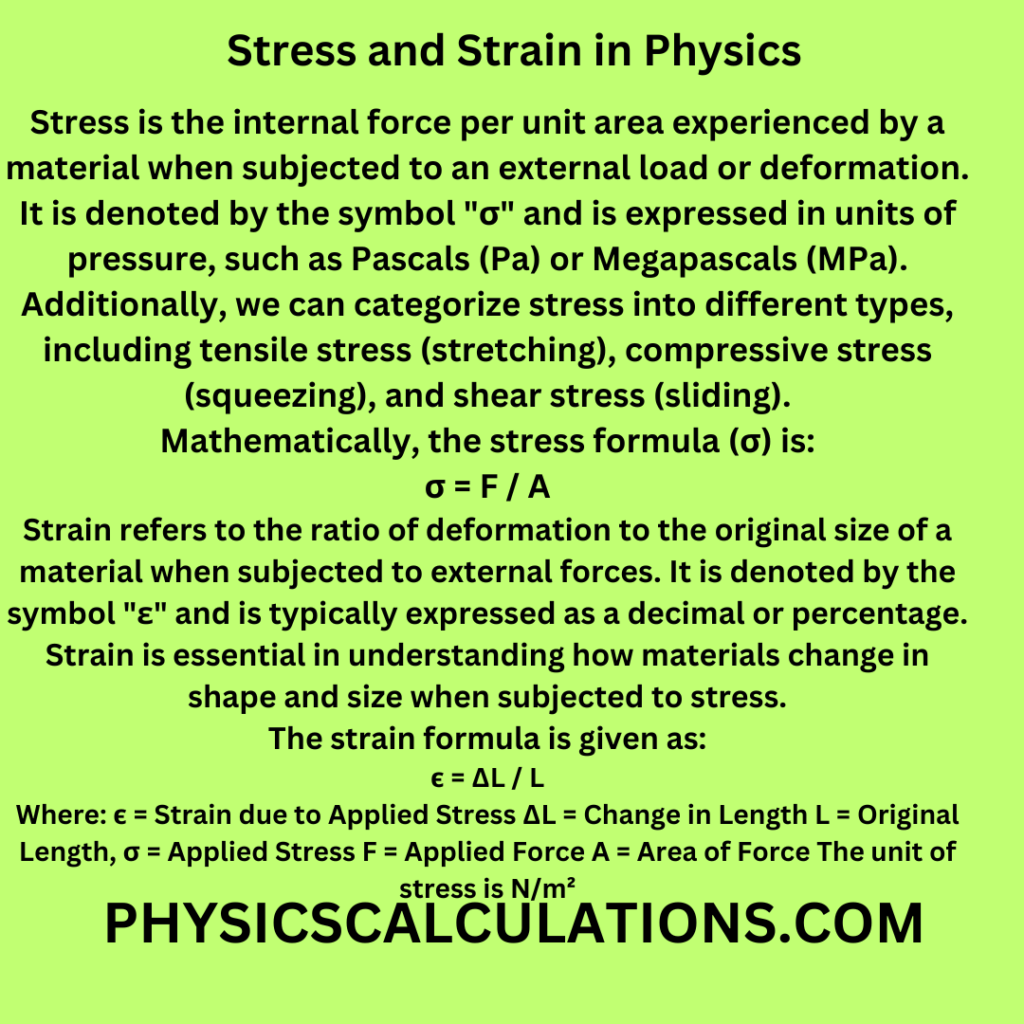
What is Stress?
Stress is the internal force per unit area experienced by a material when subjected to an external load or deformation.
The symbol for stress is “σ” and we measure it in units of pressure, such as Pascals (Pa) or Megapascals (MPa).
Additionally, we can categorize stress into different types, including tensile stress (stretching), compressive stress (squeezing), and shear stress (sliding).
Mathematically, the stress formula (σ) is:
σ = F / A
Where: σ = Applied Stress F = Applied Force A = Area of Force The unit of stress is N/m² (Newton per square meter).
Types of Stress
The various types of stress are as follows:
1. Tensile Stress
Tensile stress arises when a material experiences stretching forces. Additionally, tensile stress occurs when an external force is applied per unit area, leading to the stretching of the material.
Therefore, to calculate tensile stress, We apply the formula:
Tensile Stress (σ) = Force (F) / Cross-Sectional Area (A)
2. Compressive Stress
Compressive stress occurs when a material experiences compressive forces. When a force acts on a body, causing a reduction in its volume and resulting in deformation, it is termed compressive stress.
Additionally, the formula for calculating compressive stress is:
Compressive Stress (σ) = Force (F) / Cross-Sectional Area (A)
3. Shear Stress
Shear stress occurs when forces act parallel to each other but in opposite directions, leading to the material’s sliding or deformation. The formula used to calculate shear stress is:
Shear Stress (τ) = Force (F) / Area (A)
What is Strain?
Strain refers to the ratio of deformation to the original size of a material when subjected to external forces. The symbol for strain is “ε” and is in decimal or percentage.
Additionally, strain is essential in understanding how materials change in shape and size when subjected to stress.
The strain formula is:
ϵ = ΔL / L
Where: ϵ = Strain due to Applied Stress ΔL = Change in Length L = Original Length
Types of Strain
We can categorize strain into Compressive Strain and Tensile Strain:
- Compressive Strain: Compressive strain occurs when an object experiences deformation due to compressive stress, decreasing its length.
- Tensile Strain: Tensile strain is observed when an object undergoes an increase in length due to tensile stress.
In simple terms, we can define strain as the ratio of body extension to the original length.
The mathematical expression for strain is
Strain = Extension (increase in length) / Original length
Extension or Increase in length = E
Original length = L
Video Explanation of Stress and Strain
Solved Problems
Problem 1:
A piece of rubber 0.2m long stretches by 0.01m when a load is hung on it. Calculate the strain.
Solution:
Data:
Original length (L) = 0.2
The extension (E) = 0.01
But, Strain = Extension (increase in length) / Original length
Thus, Strain = L / E
By substituting our figures into the main formula, Strain = 0.01 / 0.2
Which implies that
Strain = 0.05
Problem 2
A force of 40N is applied at the end of a wire of length 4m and diameter 2.00 mm process and extension of 0.24mm. Calculate the
a. Stress on the wire
b. Strain in the wire
c. Young’s Modulus for the material of the wire
Data: Information from the question
Force (F) = 40 N
Length (l) = 4 m
Diameter (d) = 2.00 mm. Therefore, the radius will now become r = (2.00mm / 2) = 1.00 mm = 0.001 m
e = 0.24 mm = 2.4 x 10-4 m
Unknown: What we need to find
a. stress = ?
b. strain = ?
c. Young’s modulus
Formula: The equations that will help us solve the problems
a . stress = Force / Area = F / πr2
b. Strain = extension / length = e / l
c. Young’s modulus = stress / strain
Solution
a. Using the formula and the data provided above, we will have
Stress = Force / Area = F / πr2 = 40 / (3.142 x (0.001)2)
Thus, stress = 12.74 x 106 N/m2
b. Applying the same logic, we will have
Strain = extension / length = e / l = (2.4 x 10-4) / 4 = 6.0 x 10-5
c. Young’s Modulus = stress / strain = (12.74 x 106) / (6.0 x 10-5) = 2.12 x 1011 N/m2
Problem 3
A piece of rubber 10 cm long stretches 6 mm when a load of 100 N is hung from it. What is the strain?
Data: The information available from the question
Original length (L) = 10 cm = 0.1 m
Extension (e) = 0.006 m
Unknown: What we need to find from the question
Strain = ?
Formula: The equation we need to apply to solve the problem
Strain = extension / length = e / l
Solution
Strain = e / l = 0.006 / 0.1 = 0.06 = 6.0 x 10-2
Problem 4
If the stress on a wire is 107 N/m2 and the wire is stretched from its original length of 10.0 cm to 10.05 cm. The Young’s modulus of the wire is
Data: The information from the question
stress = 107 N/m2
Original length (L) = 10.0 cm
Extension (e) = 10.05 cm
Unknown: What we need to find
Young’s Modulus = ?
Formula: The equation that can help us solve the problem
Step 1: Strain = e/L
Step 2: Young’s Modulus = stress / strain
Solution
Step 1
Strain = e / l = 10.05 / 10.00 = 1.005
Step 2
Young’s modulus = stress / strain = (107 N/m2) / 1.005 = 9.95 x 106 N/m2
Points to Note:
Here are some vital points to note under elasticity:
Elasticity: Is the ability of a body to regain its original shape and size after undergoing distortion.
Elastic Limit: It’s the maximum stretching power of a wire.
Deformation: This usually occurs when an object is stretched or compressed. It is Plastic if the object does not regain its original shape or size. While it’s Elastic if the object regains its original shape or size.
Breaking Point: When you stretch an object beyond its limit, the object might break in the process.
How can you describe Yield Point
Yield point: It is a point when you stretch an object beyond elastic limit and in the process, the body can no longer regain its original position.
State Hooke’s Law
According to Robert Hooke, “When a body is stretched, the extension of a wire is directly proportional to the load or force applied to its end, provided the elastic limit is not exceeded”.
Additionally, it is a fundamental principle that governs the behaviour of many materials when subjected to small deformations. Therefore, Hooke’s Law states that the stress applied to a material is directly proportional to the strain it experiences, provided the material remains within its elastic limit. Mathematically, Hooke’s Law can be expressed as:
σ = E * ε
where:
- σ is the stress,
- E is the modulus of elasticity (also known as Young’s modulus), and
- ε is the strain.
Stress-Strain Curve and Yield Point
A stress-strain curve is a graphical representation of a material’s mechanical properties under tension or compression.
This curve showcases how stress and strain are related throughout the material’s deformation. The initial linear region of the stress-strain curve corresponds to the material obeying Hooke’s Law. As the strain increases, the curve deviates from linearity, indicating that the material is undergoing plastic deformation. The point at which the curve deviates is known as the yield point. The yield point is the stress level at which a material transitions from elastic to plastic behavior. Beyond the yield point, the material experiences permanent deformation, and it will not return to its original shape even after removing the load. The yield strength of a material is the stress at the yield point.
Modulus of Elasticity (Young’s Modulus)
The modulus of elasticity, also known as Young’s modulus (E), is a material property that quantifies its stiffness or ability to resist deformation under stress. It is an essential parameter used in engineering calculations and design processes. Young’s modulus is calculated as the ratio of stress to strain within the material’s elastic limit. It is expressed in units of pressure, such as Pascals (Pa) or Gigapascals (GPa). Different materials have different Young’s modulus values, which influence their behavior when subjected to external forces.
Shear Modulus (Modulus of Rigidity)
The shear modulus, also known as the modulus of rigidity (G), is another important material property related to stress and strain. It describes a material’s response to shear stress, which is the type of stress that occurs when two forces act parallel to each other but in opposite directions. The shear modulus is a measure of a material’s resistance to shear deformation. It is calculated as the ratio of shear stress to shear strain and is expressed in the same units as Young’s modulus.
Poisson’s Ratio
Poisson’s ratio (ν) is a dimensionless quantity that describes the lateral contraction of a material when subjected to axial strain. It quantifies the relationship between the strain in the direction of the applied force and the strain perpendicular to that direction. Poisson’s ratio ranges from -1 to 0.5, depending on the material. For most materials, it is positive, indicating that they contract laterally when stretched axially. However, some materials, like certain types of rubber, exhibit negative Poisson’s ratios, meaning they expand laterally under axial tension.
Bulk Modulus
The bulk modulus (K) is a measure of a material’s response to uniform compression. It quantifies the material’s ability to withstand changes in volume when subjected to pressure. The bulk modulus is calculated as the ratio of the change in pressure to the fractional change in volume. It is used in various engineering applications, such as understanding the behavior of fluids and gases under pressure.
Significance of Stress and Strain in Engineering
Stress and strain concepts are of paramount importance in engineering and design. Engineers use these principles to analyze the structural integrity of buildings, bridges, and other constructions. By understanding how materials respond to different loads, engineers can ensure the safety and reliability of various structures. Additionally, stress and strain calculations are vital in materials science and manufacturing processes. They help researchers select suitable materials for specific applications, such as aerospace, automotive, and medical industries.
Real-World Applications
1. Structural Engineering
Stress and strain analysis play a vital role in designing safe and stable structures that can withstand expected loads and environmental conditions.
2. Materials Science
Stress and strain analysis help us understand material properties and predict material failure under various conditions.
3. Geology
In geology, stress and strain analysis is important in understanding the behaviour of rocks and the mechanics of faulting and earthquakes.
Stress vs Strain Table
Here is a table highlighting the main differences between strain and stress:
Property | Strain | Stress |
---|---|---|
Definition | The measure of deformation or elongation of a material in response to applied forces or stresses. | The force per unit area applied to a material, causing deformation. |
Formula | Strain = (Change in length) / (Original length) | Stress = (Force applied) / (Cross-sectional area) |
Unit | Strain has no unit (dimensionless) | Stress is measured in units of pressure (e.g., Pascals, PSI) |
Measurement | Strain is usually expressed as a percentage or in decimal form. | Stress is measured in units of pressure (e.g., Pascals, PSI) |
Nature | Strain is a scalar quantity. | Stress is a vector quantity with direction and magnitude. |
Relationship | Strain is directly proportional to stress for small deformations (Hooke’s Law). | Stress causes strain in a material, and the relationship depends on the material’s elastic properties. |
Elastic Limit | Strain can exceed its elastic limit, leading to permanent deformation or failure. | Stress beyond the material’s elastic limit causes plastic deformation or failure. |
Application | Strain is used to measure the extent of deformation in materials under stress. | Stress is used to analyze how external forces affect materials and structures. |
Examples | Stretching of a rubber band. | Compression of a metal rod. |
Remember, strain and stress are related concepts in mechanics that describe the behaviour of materials under applied forces.
Therefore, strain measures the extent of deformation, while stress measures the intensity of the applied forces causing the deformation.
Young Modulus of Materials
Here is a table showing Young’s modulus (also known as the modulus of elasticity) of various materials:
Material | Young’s Modulus (E) | Unit |
---|---|---|
Steel | 200 – 210 GPa | Gigapascals (GPa) |
Aluminum | 68.9 GPa | Gigapascals (GPa) |
Copper | 117 – 130 GPa | Gigapascals (GPa) |
Glass | 50 – 90 GPa | Gigapascals (GPa) |
Concrete | 14 – 41 GPa | Gigapascals (GPa) |
Wood (along the grain) | 9 – 19 GPa | Gigapascals (GPa) |
Rubber | 0.01 – 0.1 GPa | Gigapascals (GPa) |
Nylon | 2.5 – 4 GPa | Gigapascals (GPa) |
Polystyrene (Styrofoam) | 3 GPa | Gigapascals (GPa) |
Diamond | 1050 – 1200 GPa | Gigapascals (GPa) |
Young’s modulus is a measure of a material’s stiffness and ability to resist deformation under an applied force. It is expressed in units of pressure, such as Gigapascals (GPa) in this table. Therefore, you need to understand that the values provided are approximate and can vary depending on the specific composition and treatment of the material.
Read:
How to Calculate Velocity Ratio of an Inclined Plane
You may also check:
Wokminer: Search for any type of job at any location